Retrieve, rework, reinstall
An architectural firm has demonstrated how to build a house from used, recycled and reusable materials. Due to the scarcity of data, this required a flexibility that is likely to change the planning process in the future.
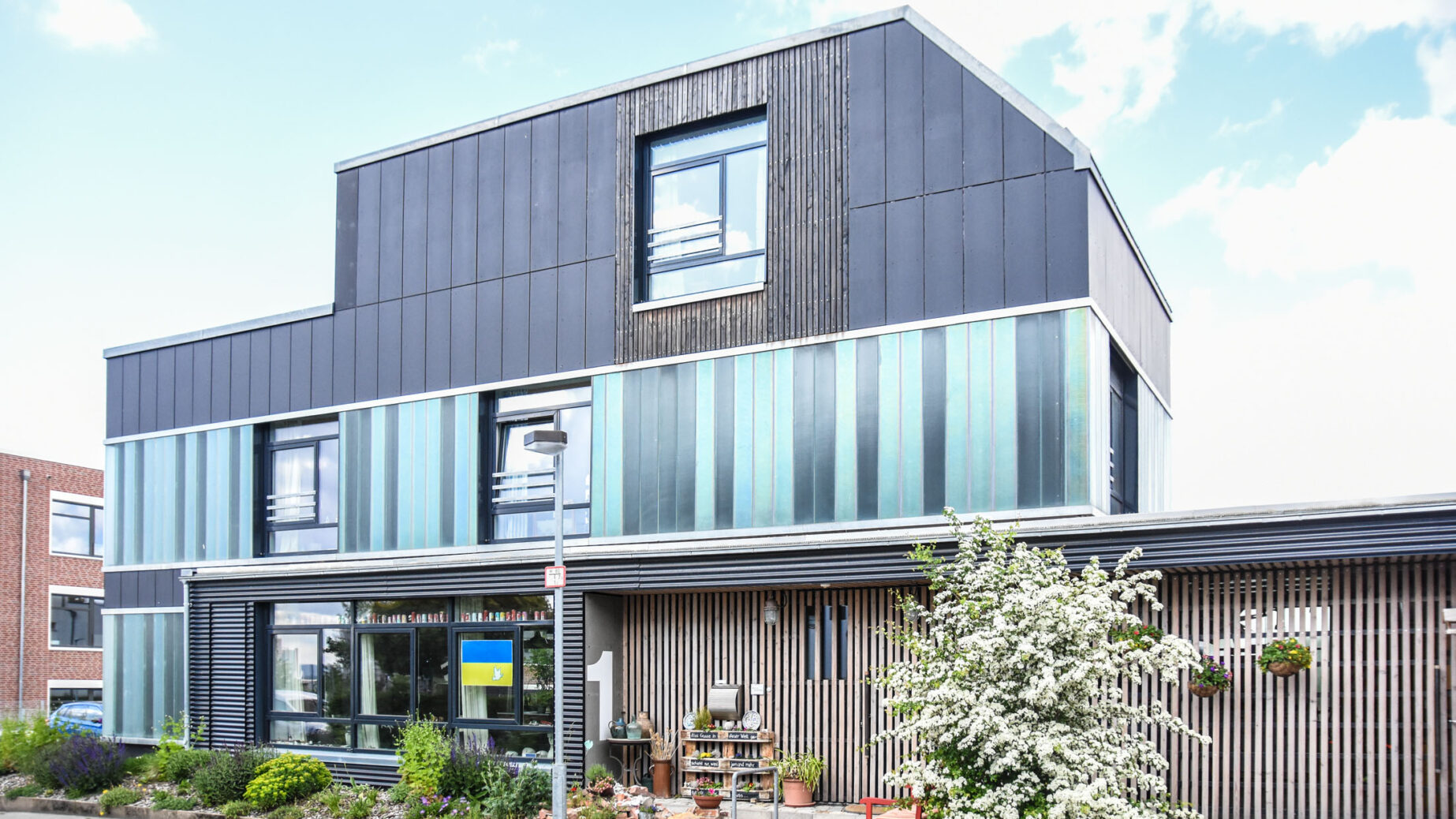
Whether you build a conventional house or one that fulfils the criteria of the circular economy, urban mining and cradle to cradle makes a big difference at many points from planning to completion. To find out what this means in concrete terms, however, you first have to build this type of house. This is exactly what the Cityförster architecture firm set out to do with the recycling house, designing an experimental residential building and overseeing its construction until the keys were handed over.
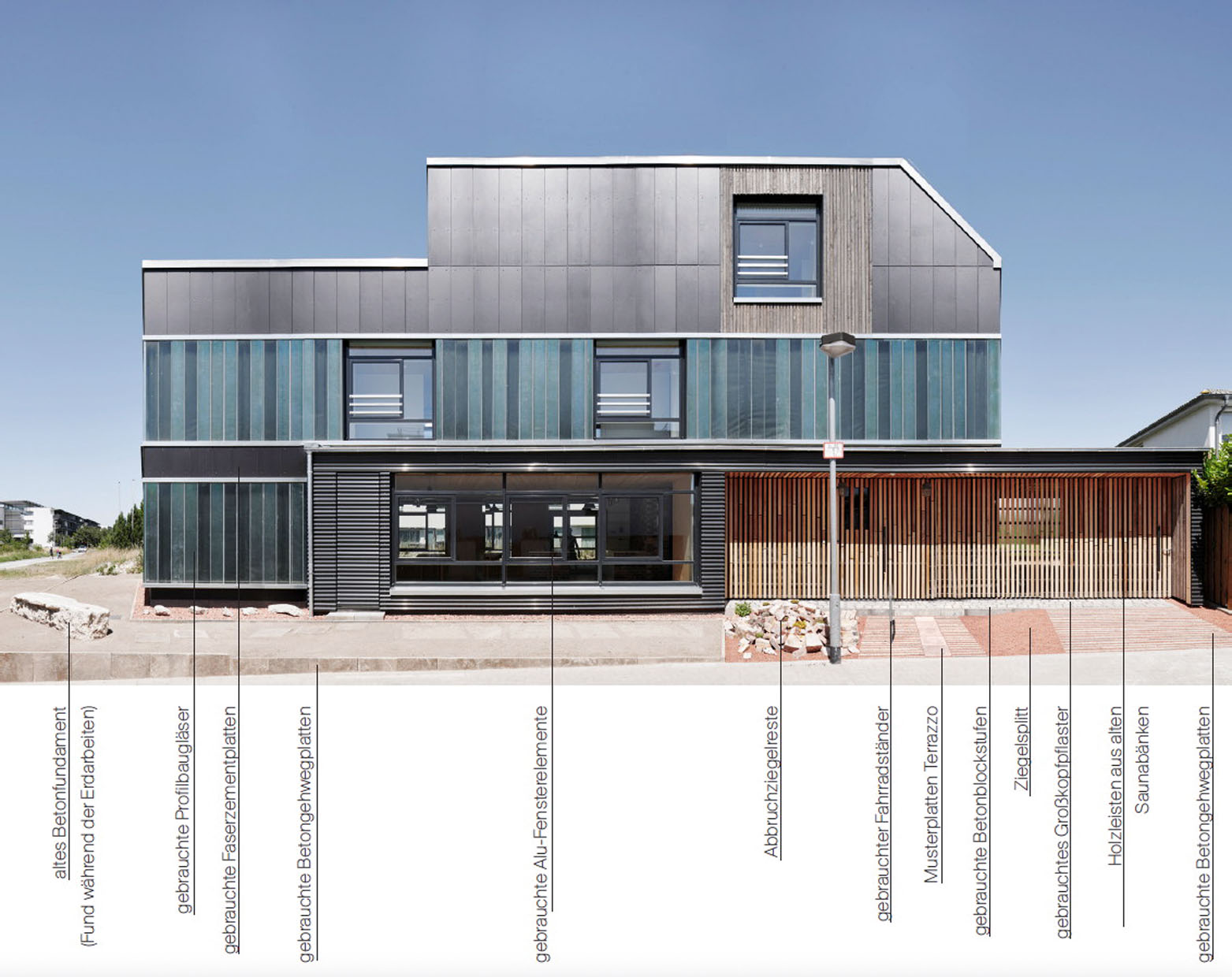
The recycling house in Hanover’s Kronsberg district was completed in summer 2019. “It is a prototype that tests the possibilities and potential of different types of recycling in a real-life laboratory and demonstrates a cycle-orientated and resource-saving planning approach,” says Nils Nolting, architect at Cityförster, who supervised the project. “We used recycled and reclaimed materials to an extent not seen in any other building in Germany up to the time of completion.” The aim was to significantly reduce grey energy and save considerable resources in the building construction process. Cityförster drew on various sources to achieve this. In terms of the carbon footprint, including transport routes, the project also benefited from the fact that many of the components could be sourced directly in the region.
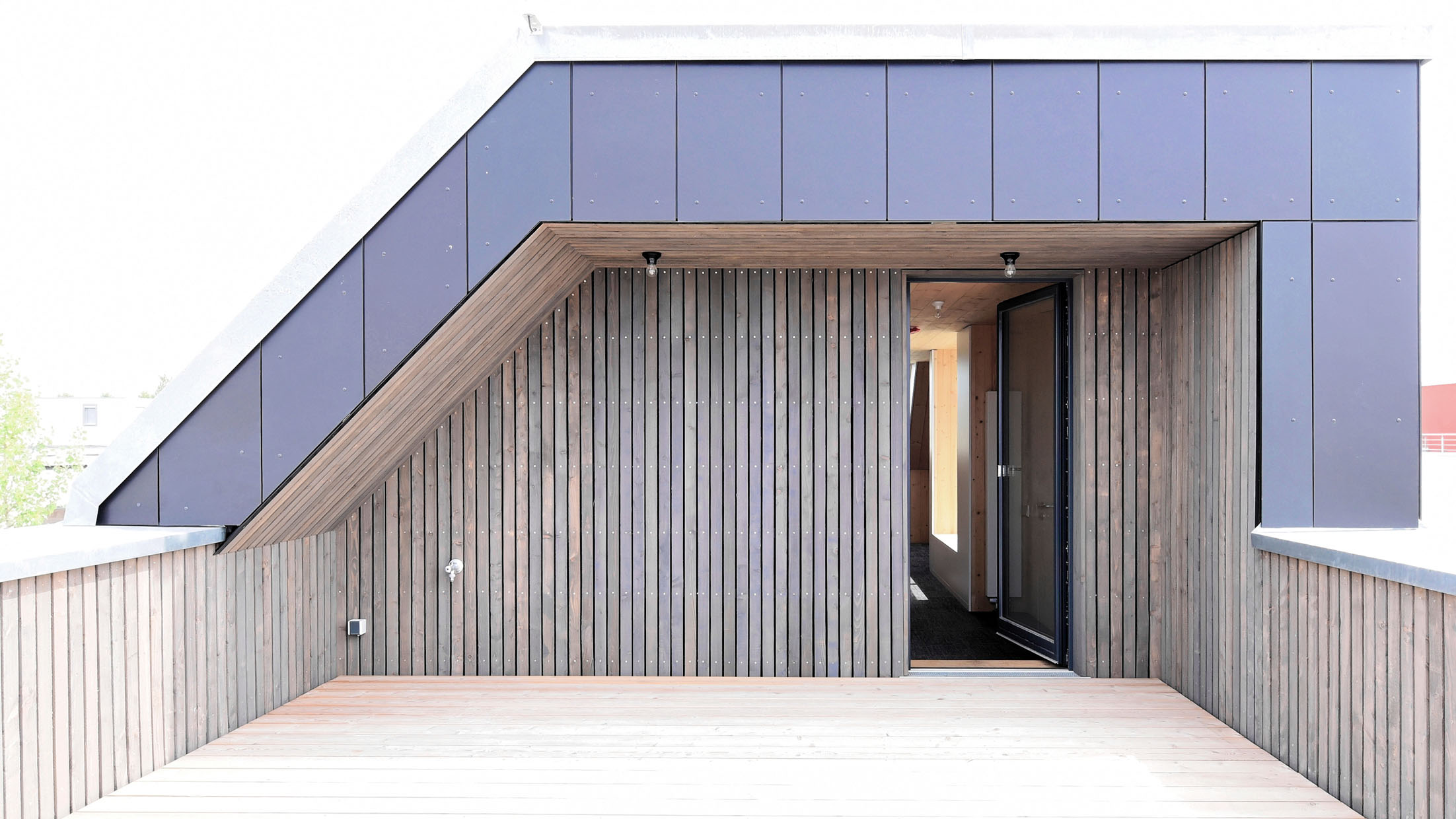
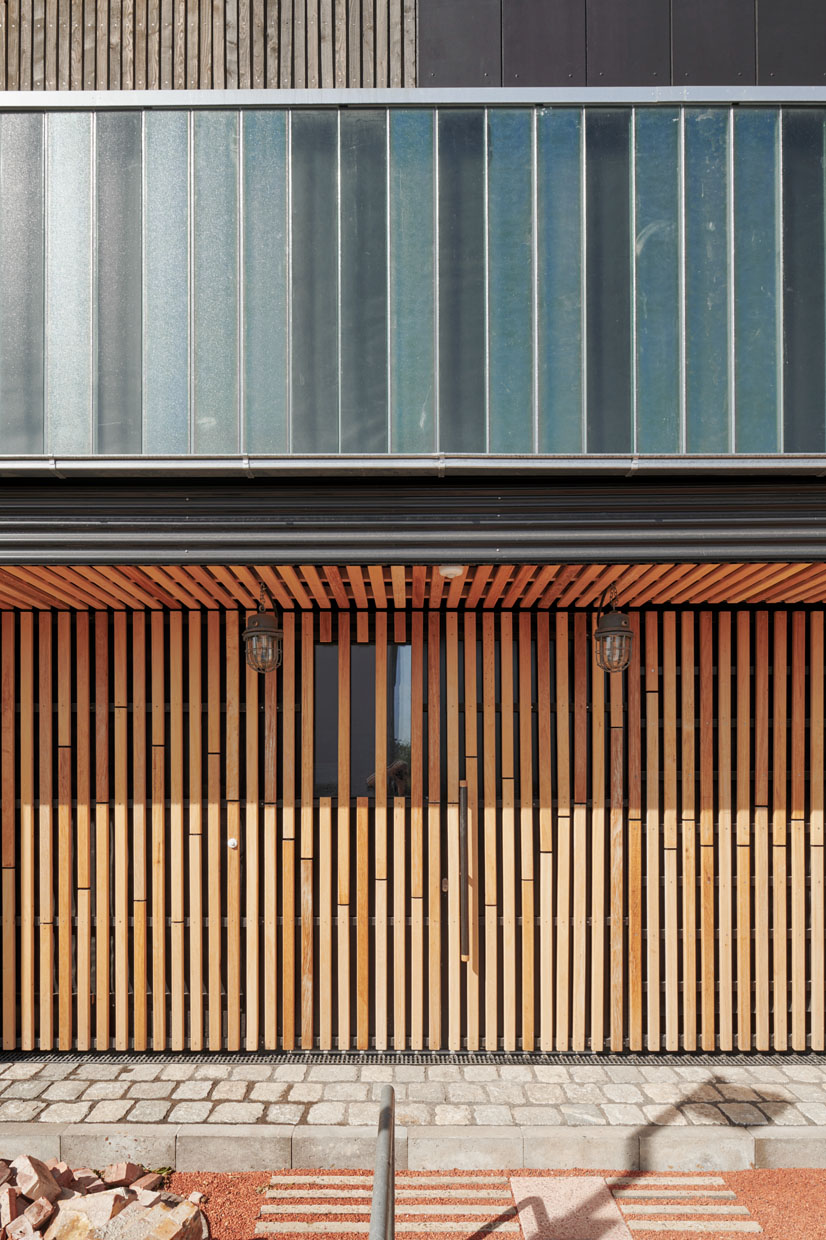
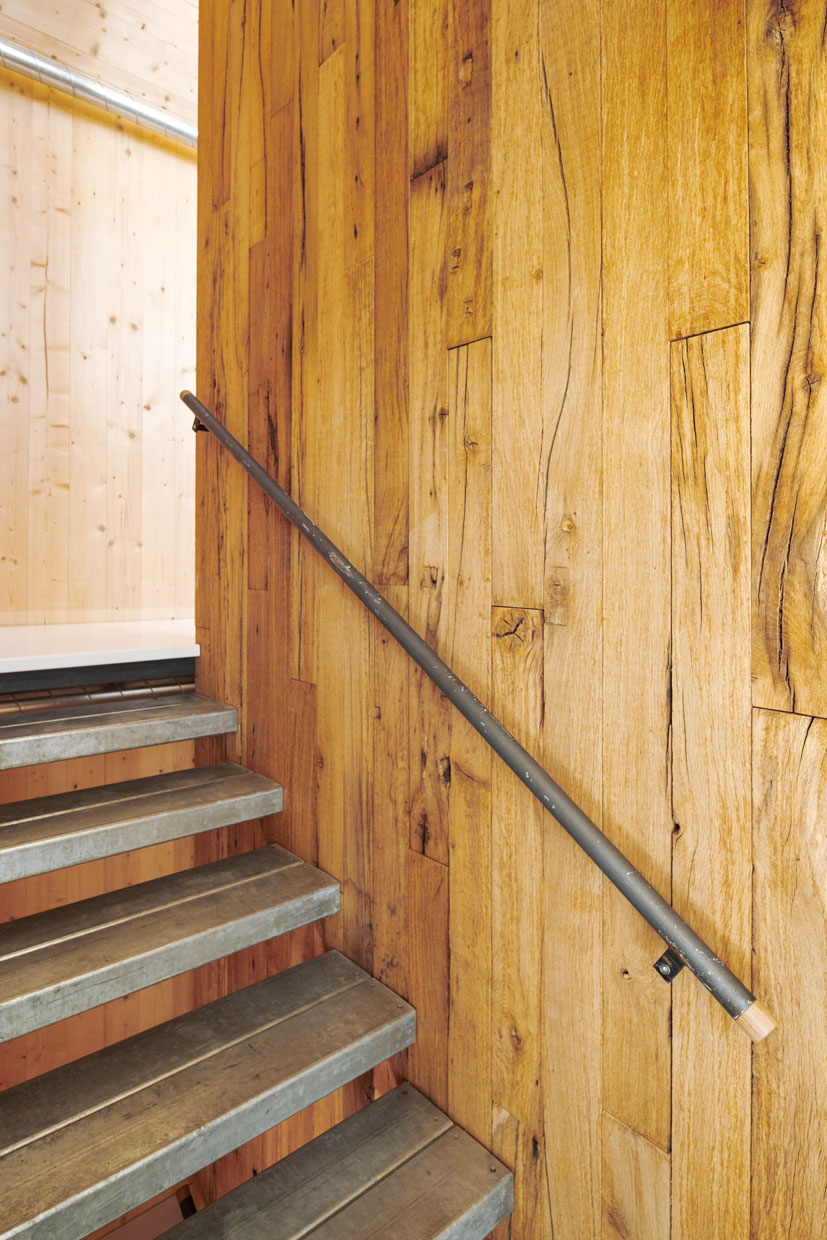
As far as possible, Cityförster initially used second-hand components. “Around 90 per cent of the façade cladding is made from used components, as are all the windows and exterior doors,” says Nolting. Recycled components and materials were also used almost entirely for the interior fit-out and outdoor areas: for example, trade fair construction panels for interior walls, floors and doors or used concrete paving slabs as screed replacements on board pile ceilings and as lawn stones, kerbs and walls.
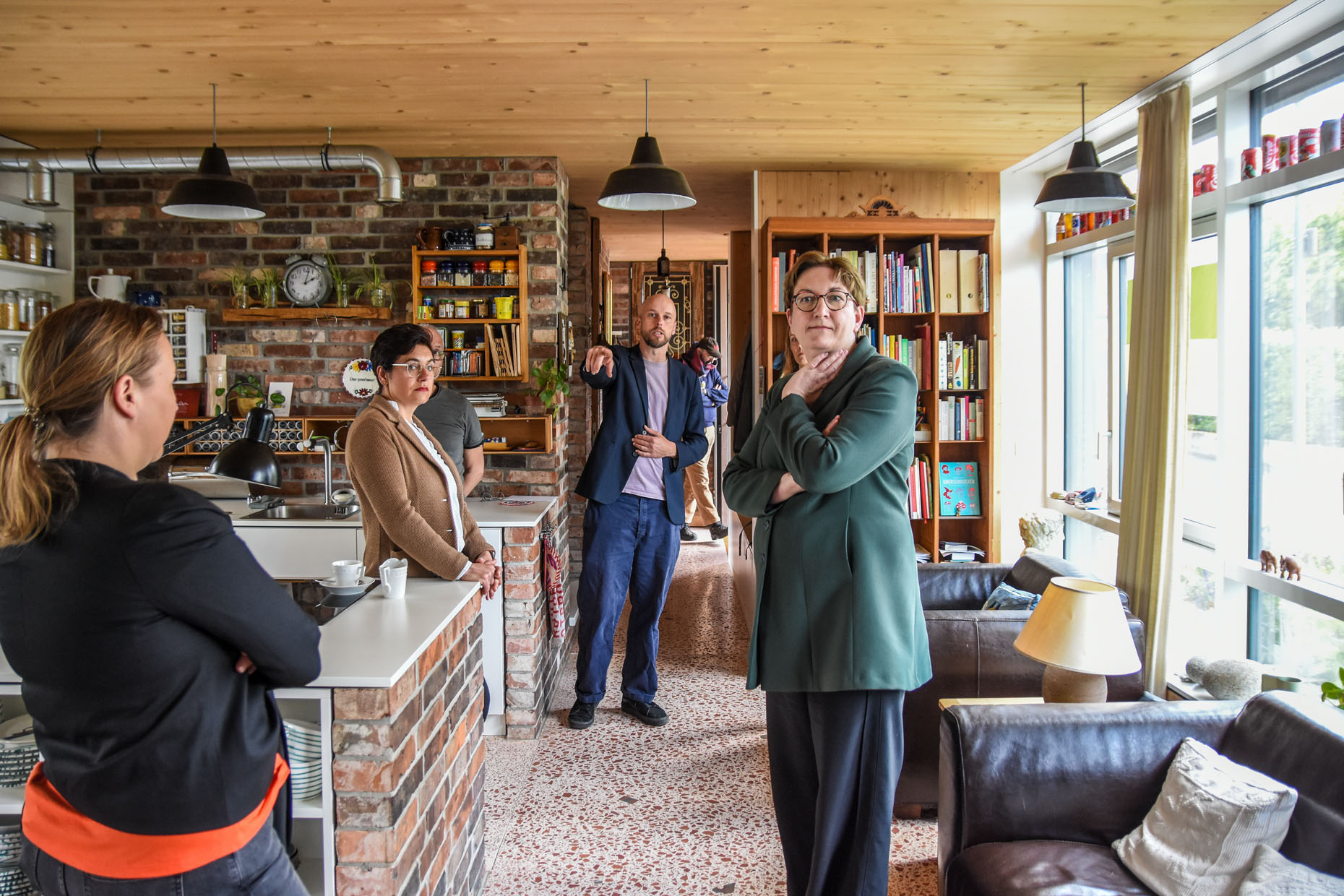
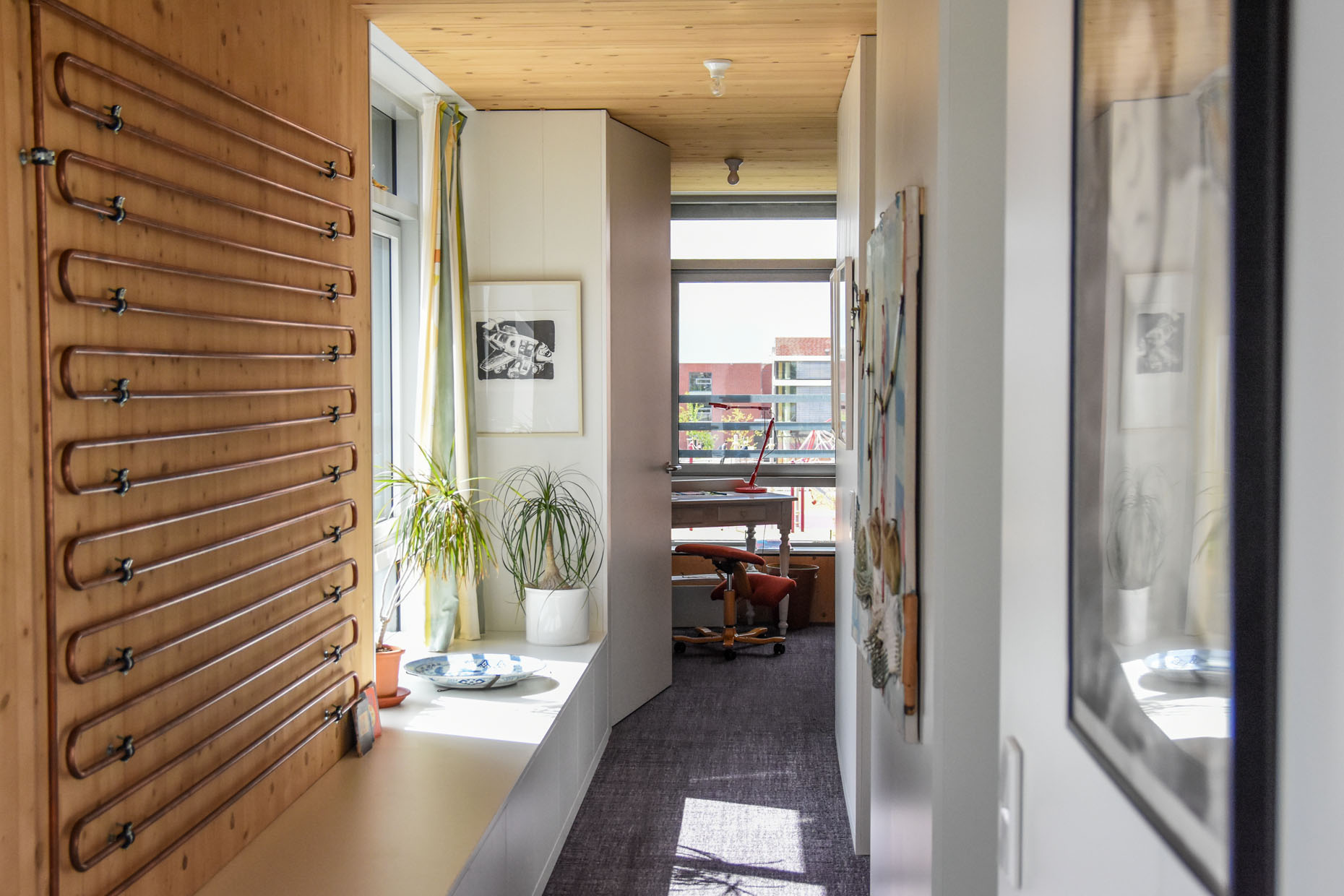
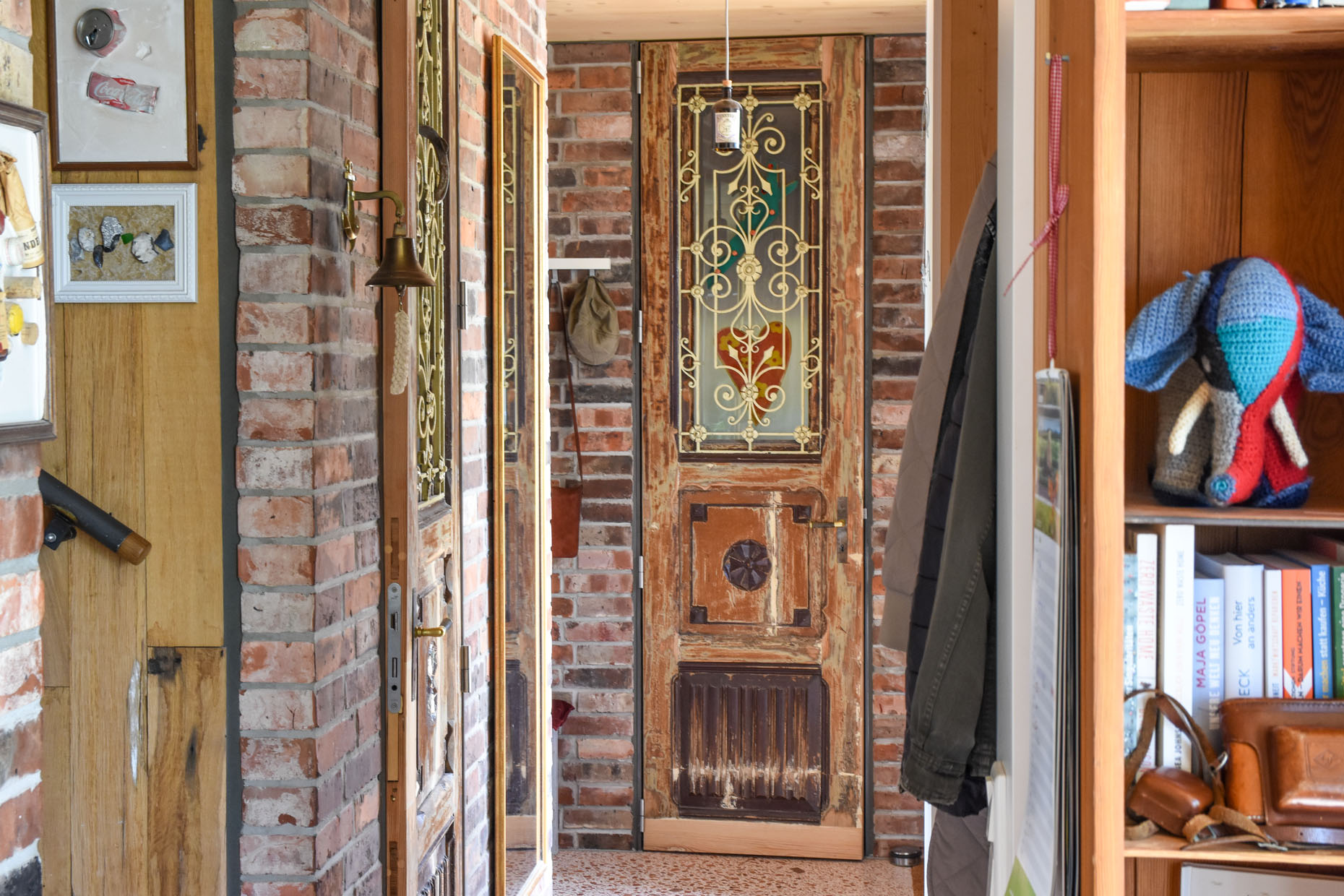
Packing, storing and cleaning building materials
Between retrieval and reinstallation, the components usually had to be reworked. A few examples: Profiled building glass, which is now used as façade cladding, was in the meantime packed, stored, cleaned and sorted before installation; window elements were upgraded for energy efficiency with 3-pane glazing before installation. Various steel U-profiles also had to be stored temporarily after removal before they were cut to size. They now serve as fall protection in the stairwell, as a substructure for stair landings and as steel frames for floor-to-ceiling doors.
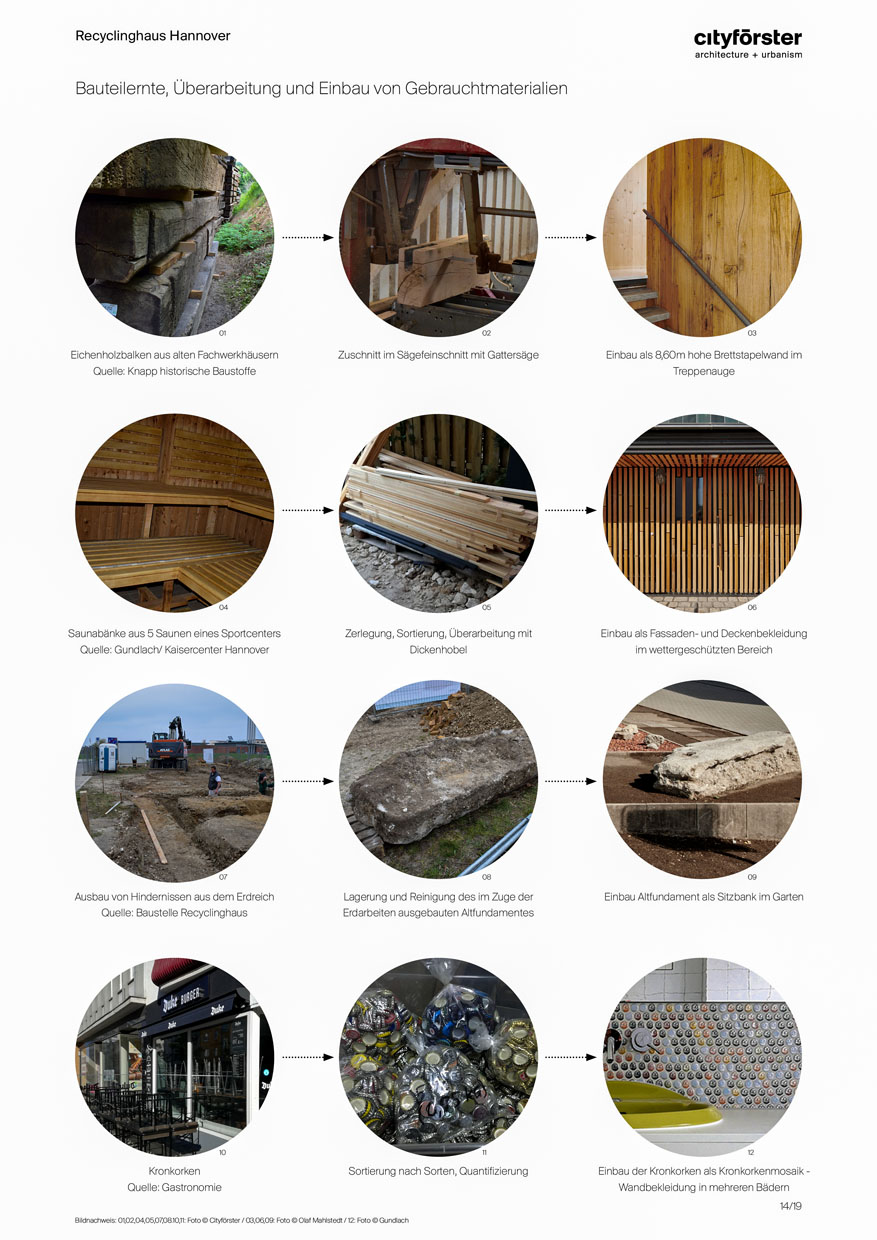
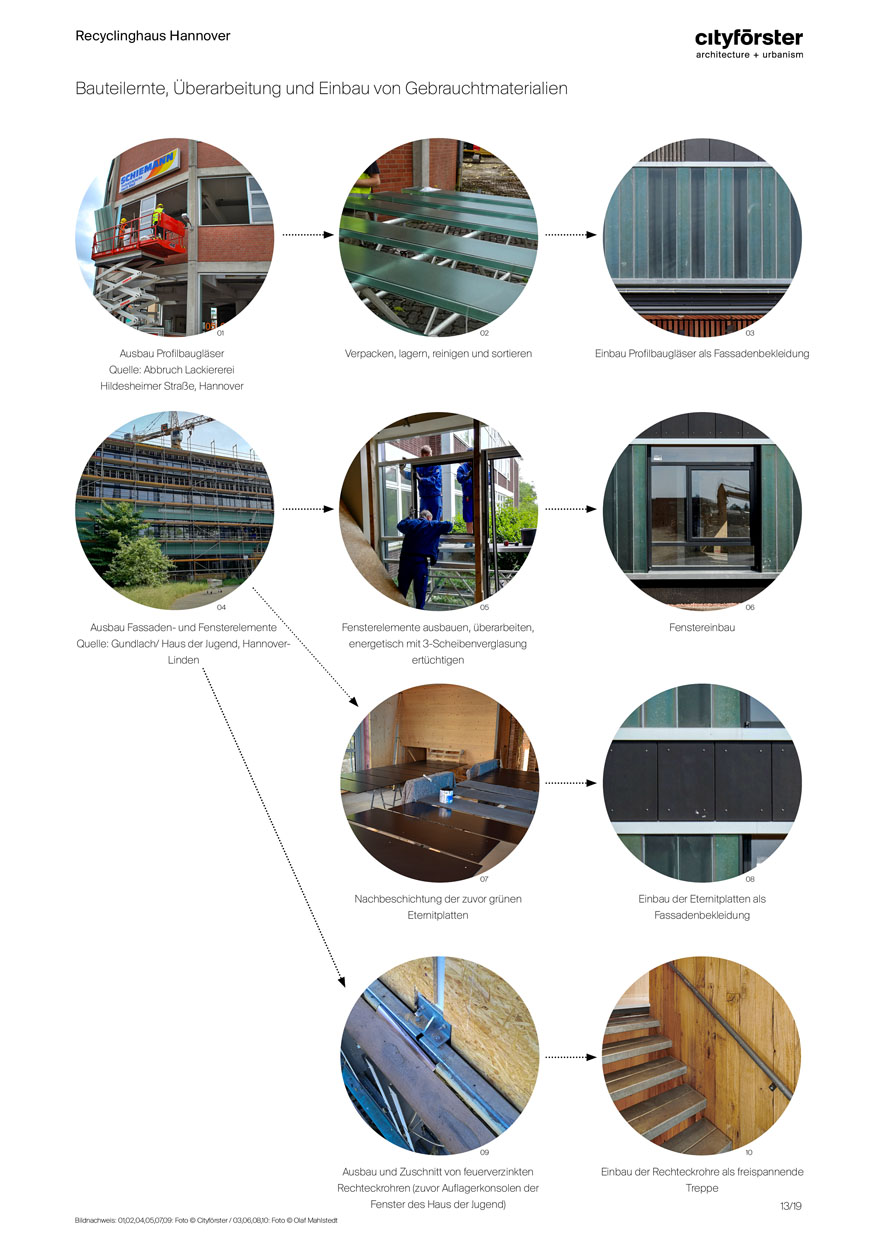
Where Cityförster was unable to find used components, the team used recycled building materials from the building materials market: including various products from glass recycling (foam glass gravel, granulate and panels), various recycled chippings and façade insulation made from recycled cocoa bean jute sacks. “We also used industrially recycled materials,” explains Nolting. “The foundation made from recycled concrete was the first to be approved in Lower Saxony.” If material had to be supplemented elsewhere, the team used recyclable building products. “Like most building products, we installed the shell made of glue-free solid wood elements in a recyclable way” says Nolting. “This means that when they are dismantled, they can be broken down into their component parts again without any loss of quality.” Circular construction site organisation also meant using almost all the leftover materials from the construction process.
Working through the service phases in a non-linear way
“Designing and constructing against the backdrop of limited availability of resources, raw materials and building materials places completely different demands on the design process than on ‘conventional planning’,” emphasises Nolting. “For example, planning with used components and their dimensions and quantities determined by the existing situation of the ‘raw material sources’ requires an agile, partly ‘reversed’ planning approach – a non-linear processing of the service phases, specific detailed solutions and special legal framework conditions.” Another challenge is the procurement of suitable used components: “ A professional used components market has so far barely been established.”
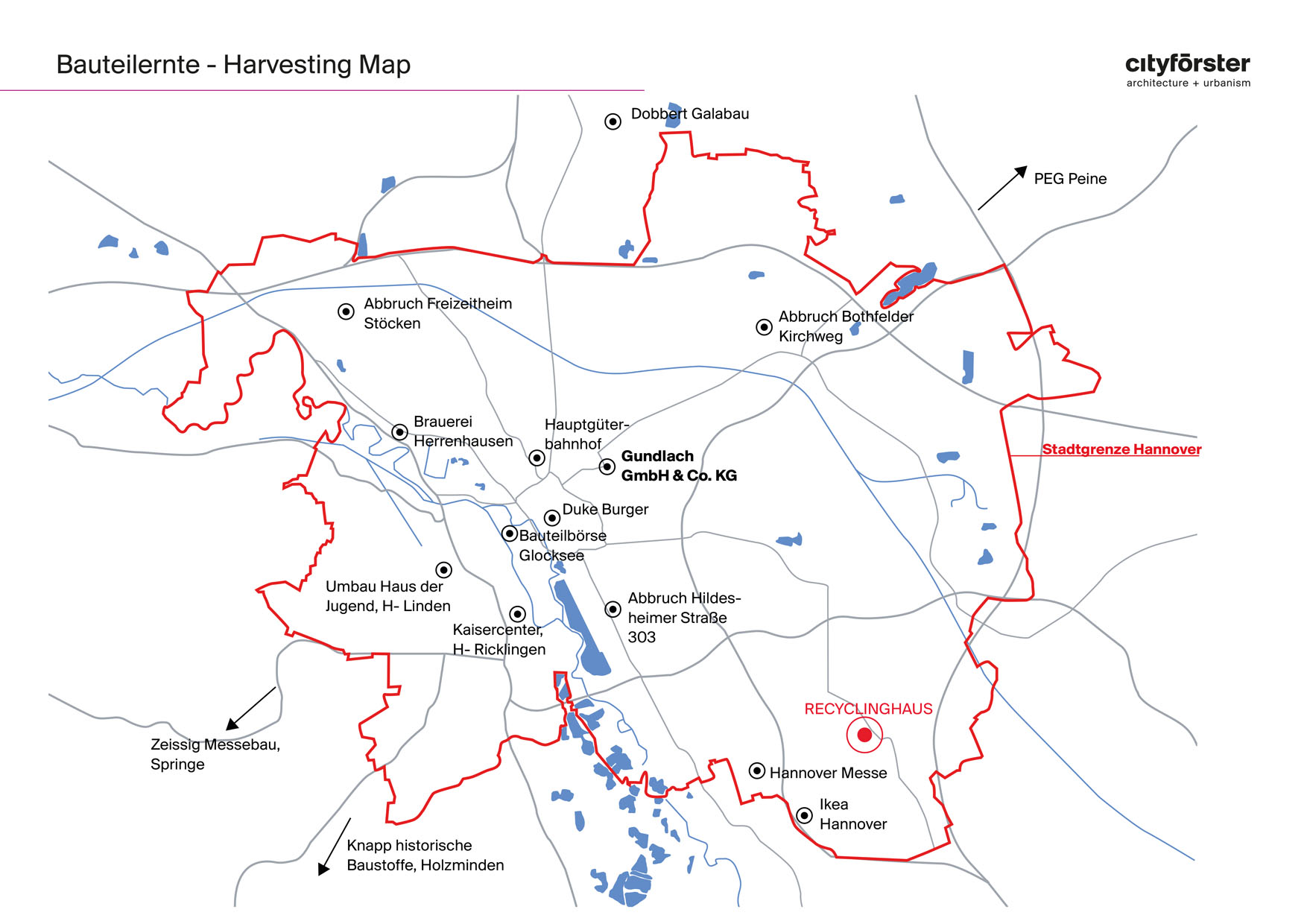
In this respect, the framework conditions for the recycled house were favourable. The client of the house, the Hanover-based housing and construction company Gundlach, was able to supply a large proportion of the used components itself. Their own stock, demolition and remodelling projects provided a really good material basis for the project – an important prerequisite for the success of the project. “We had direct access to used building materials with knowledge of their availability in terms of time and quantity,” explains Nolting. “We were also able to verify the material properties of the components based on the available documentation on our own building stock.” The data on used components plays an important role, as it must be possible to plan with the used components. “For this, it is helpful or even necessary that dimensions, construction drawings, U-values, etc. are known or can be obtained,” emphasises Nolting. “In addition, all components must be approved and their product properties must be verifiable, for example by means of conformity marks, delivery notes and data sheets.”
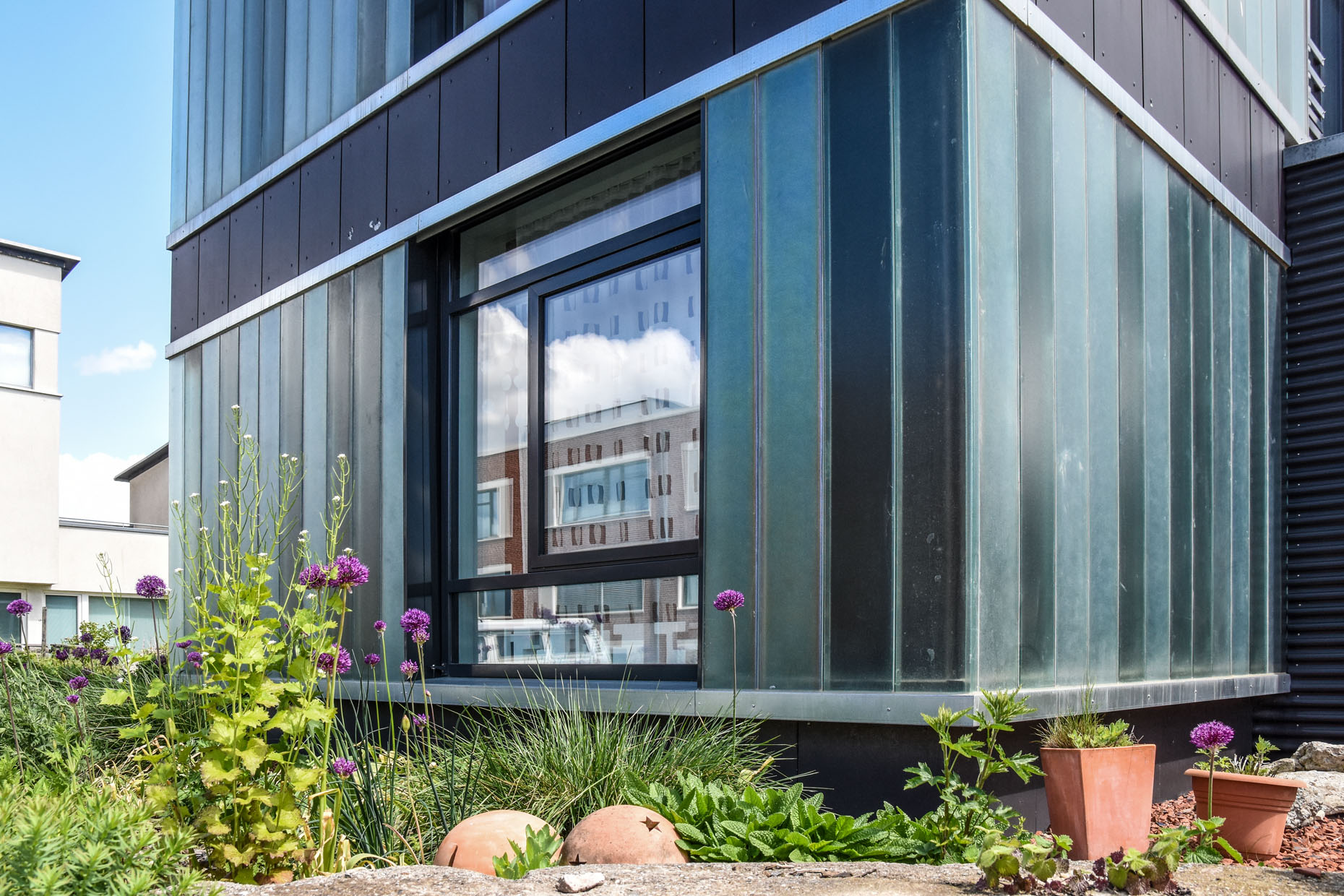
Planning the shell construction starting from the windows
Once the Cityförster team had established the basic planning parameters and identified material sources, the detailed planning began with used components. “This required new design methods,” says Nolting. “We had to translate the ‘coincidence’ of the available building materials with their specified quantities and dimensions into dedicated planning – similar to a jigsaw puzzle.” This resulted in unexpected design and functional benefits during the construction process. As an example of a temporal, non-linear shift in planning services, Nolting cites the element planning of the solid timber shell construction in combination with used components: “We had to plan the shell construction at an early stage based on the existing, unchangeable dimensions of the used window elements and the façade cladding made from used materials.” Once the approval planning had been finalised, the extended building shell (shell, façades, roof) was determined. At this point, it was also clear which materials were suitable for which use – and above all: that they were available. Then construction began. “Many other design decisions – such as those relating to the interior fit-out and open space design – were made gradually during the construction phase,” says Nolting. “In some cases, we also had to react to the changing availability of building materials over time.” The building was therefore further designed during the construction process.
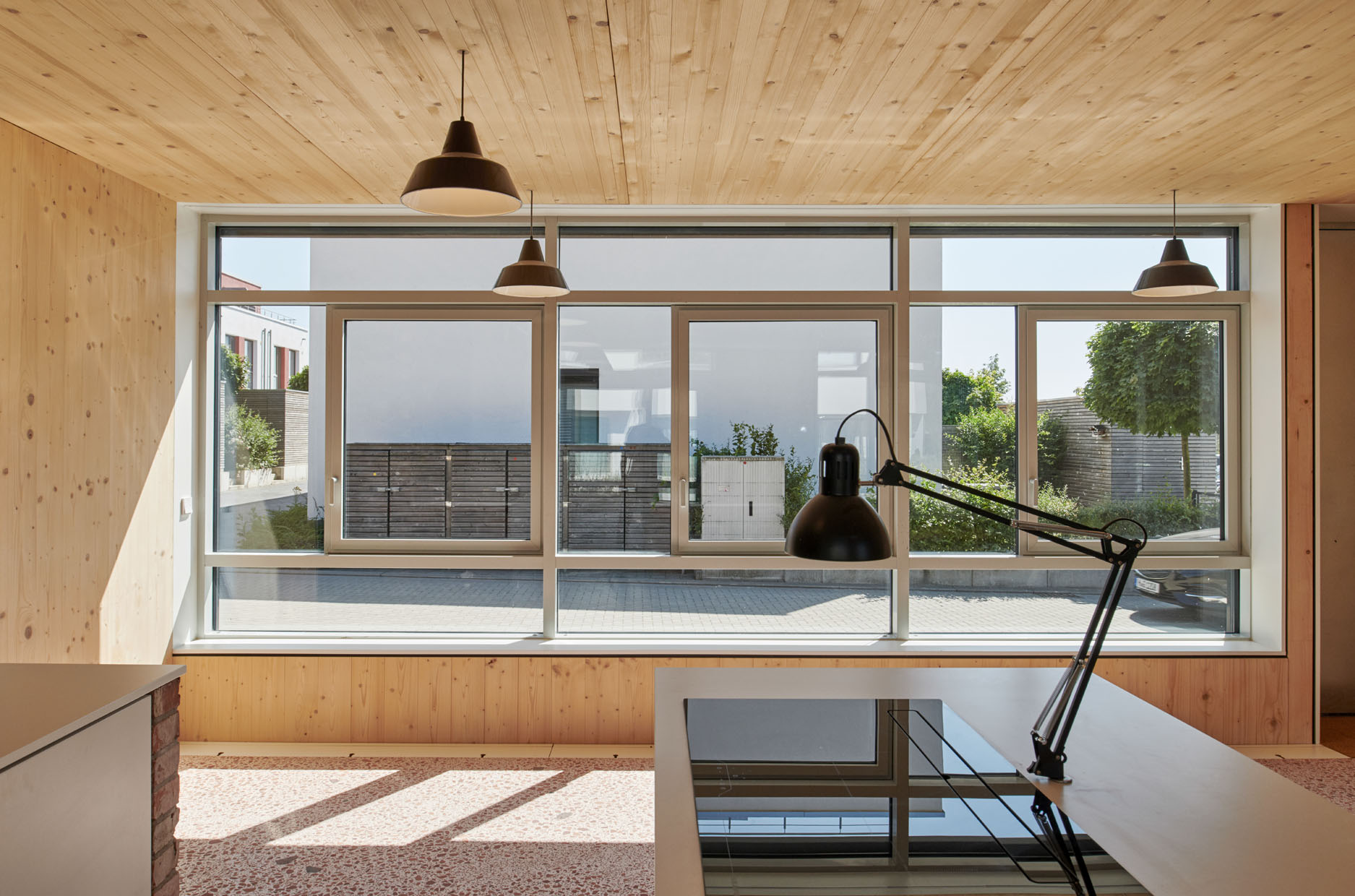
Between scarcity and abundance
“The ‘quantity game’ also played a role here – in other words, too little and too much of the materials used for the respective planned purpose,” explains Nolting. “We were able to compensate for insufficient quantities of materials by using other available materials in ‘missing places’.” If larger than required quantities of certain materials were available, the team was able to either create additional, originally unplanned added value on the building itself – or find uses for leftover materials in other construction projects.
“In order to enable the reuse of components on a broader basis in the future, we need access to information about the properties and – timely! – availability,” summarises Nolting. “Component information could also be disclosed as part of a demolition notice. This would also make components available on a larger scale for circular reuse.”
Smaller architectural firms and developers will have to be patient until the necessary infrastructure has been developed to build houses according to the criteria of the circular economy, urban mining and cradle to cradle with similar effort applied in conventional projects. Nevertheless, there are already sources of used and recycled building materials in many regions. Early research at component exchanges and online marketplaces is worthwhile in order to plan and construct at least parts of a building sustainably.
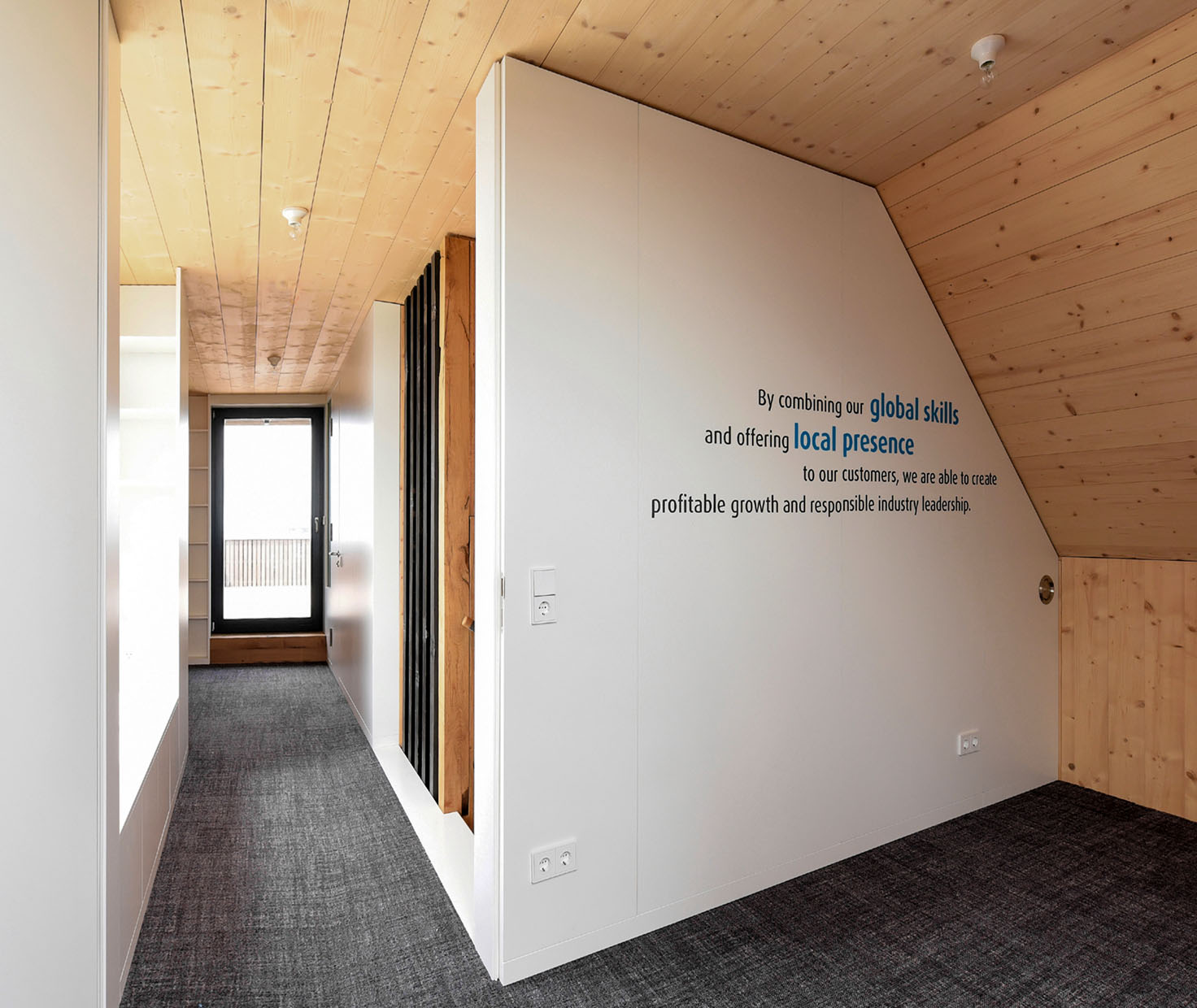
House & energy
A living space of around 156 square metres extends over two full storeys and a staggered storey. Attention was also paid to energy efficiency in terms of operation. Despite the extensive use of recycled components, the house achieves an energy standard of at least KfW Efficiency House 55. In addition to the insulation, the building services contribute to this: An air-to-water heat pump with solar thermal support heats the building, accompanied by a controlled domestic ventilation system with heat recovery.
Text: Lars Klaaßen, March 2024
Photos: © Olaf Mahlstedt, Sascha Priesemann/ Fa. Gundlach, Hans Schaper/ Fa. Gundlach, Cityförster Architekten
About the author:
Lars Klaaßen, journalist, has been working as a freelance author and editor — among others for taz, Süddeutsche Zeitung, Deutsches Architektenblatt and scientific institutions — since 1989. He specialises in the fields of architecture and urban development, construction and housing as well as energy transition and climate change. www.medienbuero-mitte.de
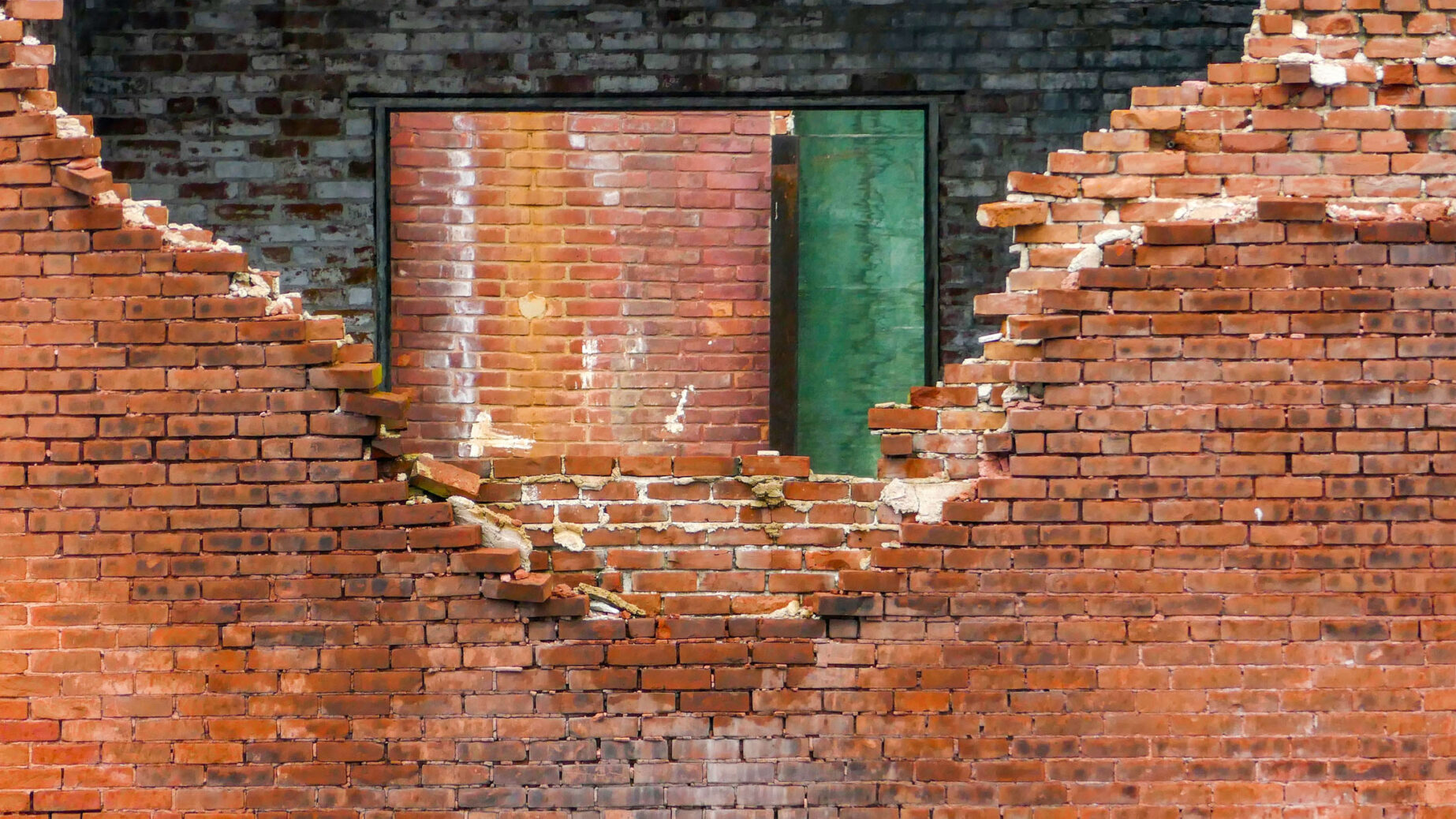
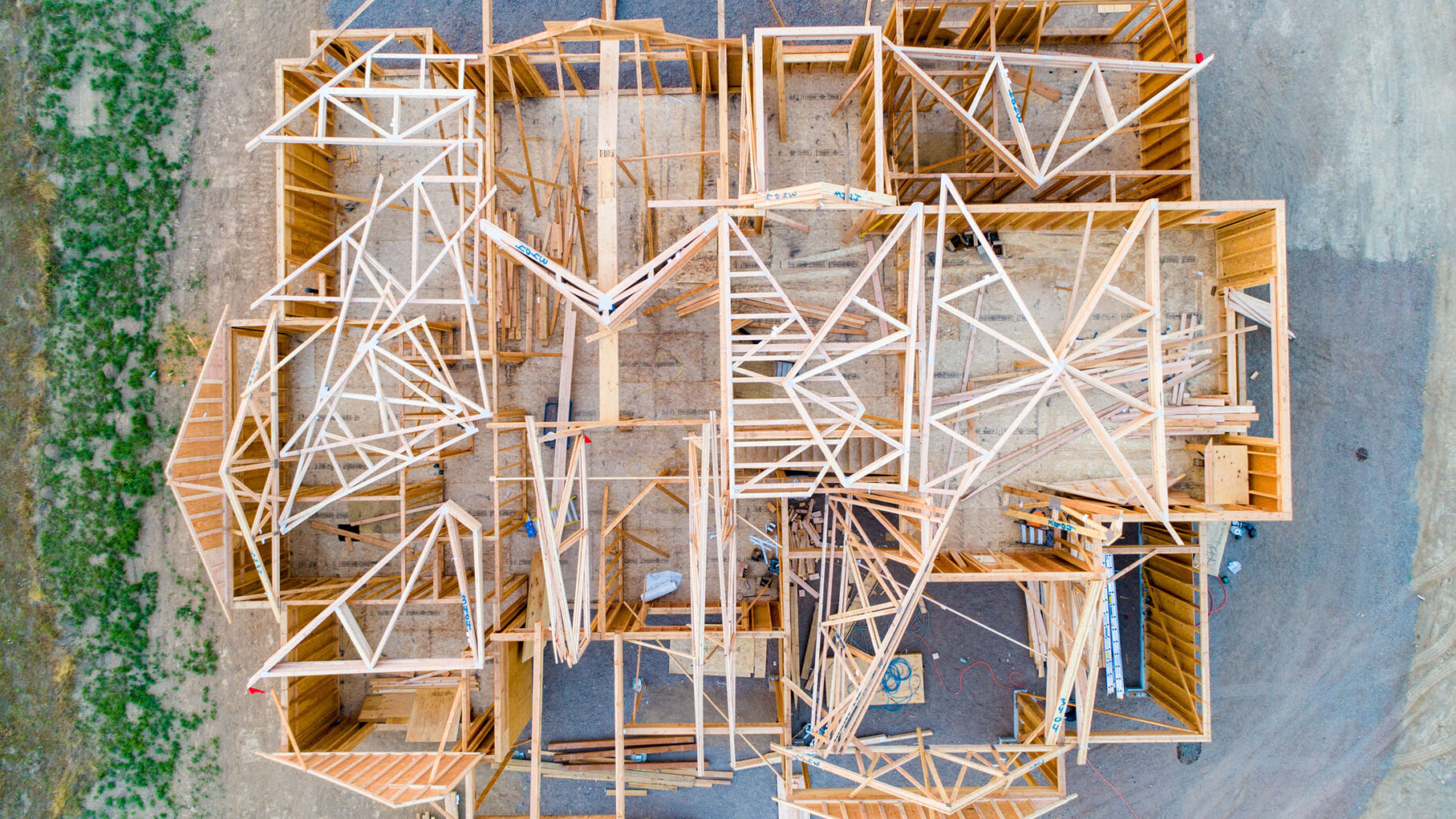
0 Comments